5 Key Considerations for Choosing a Vertical Machining Center
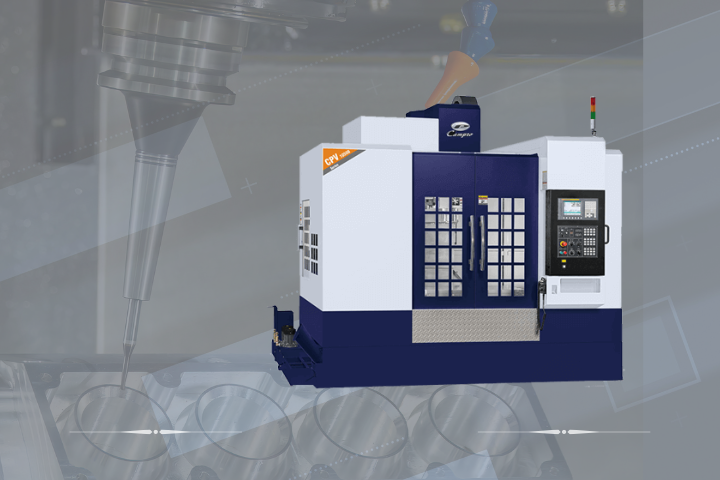
In today's rapidly changing manufacturing industry, selecting the right vertical CNC machine has become crucial for companies to enhance their competitiveness. These efficient machines not only accelerate production processes but also improve machining quality, serving as cornerstones in the automotive, aerospace, and electronics manufacturing industries. As market demands continually evolve and technology advances, companies must consider multiple factors when choosing a CNC vertical machining center. This article will explore the 5 key considerations for selecting a vertical machining center, helping companies make informed decisions to meet more precise machining requirements and achieve higher production efficiency.
Vertical Machining Center Market Trends: Future Directions and Demand
Changes in market demand are crucial factors influencing the choice of a new vertical machining center. As consumer expectations for product quality and production efficiency rise, manufacturers must assess which models can most effectively meet these needs. Modern market trends indicate a continuous rise in demand for high-performance and multifunctional vertical CNC machines. These machines can quickly adjust and maintain high production efficiency, making them particularly suitable for small-batch, diversified production models.
Technological innovation is also a key driver of changes in market demand. For example, advancements in CNC technology have improved machining precision while simplifying the operation process, making vertical machines more user-friendly. Additionally, integrating advanced measurement techniques and real-time monitoring systems allows the machine to automatically adjust parameters during the machining process, further enhancing product quality and efficiency.
Campro Machinery's Vertical Machining Center Product Line
Since 2016, Campro Machinery has actively invested in the field of intelligent machinery, starting with factory visualization management and gradually expanding to provide comprehensive smart factory solutions. We have become pioneers in the digital era by integrating advanced technologies, machine networking, and intelligent machinery, enabling machines to automatically adjust parameters during the machining process, thereby enhancing product quality and production efficiency. Campro Machinery is a professional CNC machine tool manufacturer, producing a variety of machining centers and lathes. Our vertical machining centers are divided into four categories, each with different models:
CPV-B Series #40 Box Ways Vertical Machining Center: This comprehensive machining center pursues stability and versatility. It enhances the efficiency of machines in the factory, featuring a three-axis box ways design for superior stability. The entire structure is made of high-grade cast iron and undergoes heat treatment to eliminate internal stress, ensuring optimal rigidity and precision durability. The series offers X-axis travel ranges from 850 mm to 1600 mm for customer selection.
CPV-B Series #50 Heavy Duty (Box Ways) Vertical Machining Center: In addition to stability and versatility, the #50 spindle is more suitable for heavy cutting. The series offers X-axis travel ranges from 1100 mm to 2200 mm for selection.
CNV Series High Efficiency Vertical Machining Center: Focused on economy and efficiency, this is the best choice for a wide range of small to medium-sized parts manufacturers and users pursuing high efficiency. The series offers X-axis travel ranges from 550 mm to 1300 mm for selection.
NV Series High Performance Vertical Machining Center: Compared to other linear guideway vertical machining centers of the same size on the market, the NV series offers a larger Y-axis travelling range. Its unique loop design and spindle thermal symmetry design effectively reduce thermal deformation, improving accuracy and stability. Meeting the demands of many metalworking users, this machine combines high mobility, high rigidity, and high stability. It can also add a 5-axis table to the standard worktable configuration, increasing the feasibility of different machining operations.
Our complete product line meets various functional needs, providing customers with a diverse range of options, from high precision to high efficiency, from basic to advanced models, fully covering all application requirements.
Key Considerations for Choosing a Vertical Machining Center
When selecting a vertical machining center, it is important to consider various factors to ensure that the chosen equipment meets current and future production needs.
Machining Requirements and Application Scenarios
Different industries and products have varying requirements for machining precision, speed, and flexibility. Companies should evaluate the machine’s performance and suitability based on their specific machining needs. For instance, precision machining requires equipment with high accuracy and stability, while mass production demands efficient and reliable machines.
Technical Parameters and Performance
Technical parameters are one of the core considerations when choosing a vertical machining center. These include spindle speed, travel range, rigidity, stability, and control systems. These parameters directly affect the machine’s machining capabilities and applicability.
Intelligent and Automated Functions
The demand for intelligence and automation in modern manufacturing is increasing. Machines equipped with AI integration, automation technologies, and real-time monitoring can improve production efficiency, reduce labor costs, and ensure product quality.
Brand Reputation and After-Sales Service
Choosing a brand with a good reputation ensures the quality and performance of the machine. Additionally, comprehensive after-sales service provides timely technical support and maintenance, ensuring the normal operation and longevity of the machine.
Cost-Effectiveness Analysis
Companies should conduct a cost-effectiveness analysis based on their budget. It is essential to choose a vertical machining center that offers the best value for money while meeting machining needs and technical requirements to achieve optimal investment returns.
Future Technological Developments
In terms of technological advancements in vertical machining centers, the integration of artificial intelligence (AI) is significantly enhancing the accuracy of machining decisions and optimizing production processes. AI can automatically adjust machine settings to accommodate changing machining demands, thereby increasing production efficiency and reducing human intervention.
Additionally, automation technology enables vertical machining centers to perform unattended production, which not only lowers labor costs but also improves the stability of production quality. These technologies enable machines to flexibly handle small-batch and diversified production needs, aligning with modern manufacturing's dual requirements for high efficiency and flexibility.
Success Case: Enhancing Production with Vertical Machining Centers
A well-known Taiwanese compressor manufacturer faced the challenges of enhancing production efficiency and reducing costs while maintaining high product quality and precision. To address these challenges, the company chose the NV-1280 Vertical Machining Center from Campro Machinery, equipped with 4/5-axis rotary tables, for the mass production of dynamic and static scrolls for compressors. Due to its high precision, stability, and performance, the NV-1280 was evaluated and deemed the best choice to meet the company's needs.
The customer used the NV-1280 machine for rough contour machining and fine finishing of the scrolls. These processes required extremely high-quality standards, with the contour and verticality of the scroll walls directly affecting the compressor's lifespan. The tolerance requirements were set within ±0.005mm, ensuring the compressors' stable operation and long-term durability.
After selecting the appropriate equipment, the customer achieved several significant results. Firstly, production efficiency increased substantially, leading to shorter production cycles. Secondly, the precise machining quality ensured product consistency and reliability, reducing rework and scrap rates. Lastly, significant cost savings were realized by reducing labor and material costs, enhancing market competitiveness. These improvements not only met current market demands but also prepared the company for future challenges.
Conclusion and Future Prospects for Vertical Machining Centers
When choosing a vertical machining center, it is crucial to consider how the machine can adapt to rapidly changing market demands and technological trends. Case studies have shown that selecting a vertical machining center equipped with advanced technology and flexibility is a wise investment for businesses. This not only ensures product quality and production efficiency but also prepares companies for future market challenges.
Based on the analysis presented in this article, future vertical machining centers will need to integrate AI and automation technologies more extensively to enhance operational efficiency and precision. Moreover, to meet diverse production needs, the design of these machines should focus more on modularity and scalability.
In summary, when selecting a vertical machining center, it is important to consider not only its current technical specifications and performance but also its future adaptability and development potential. Such forward-thinking will enable businesses to maintain a competitive edge in future market competition and achieve sustained business success.
To learn more about our vertical machining center, please click on the product information. If you have any product needs or questions, please feel free to contact us. We look forward to providing you with the best service.