Mastering Modern Manufacturing: The Comprehensive Guide to 5-Axis CNC Machining
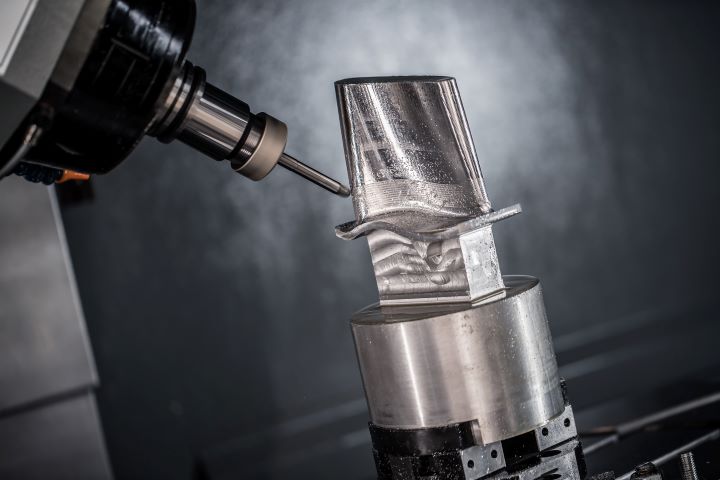
With the advancement of modern manufacturing technology, 5 axis cnc machining centers have become important tools for handling complex workpiece processing. Although traditional 3-axis and 4-axis machining has its advantages in some applications, these technologies fall short when dealing with complex geometries and high-precision workpieces. The advent of 5 axis machining centers has not only improved machining accuracy but also significantly shortened processing times, bringing more flexibility and efficiency to the manufacturing industry. This article will provide an in-depth introduction to 5 axis cnc machining centers, exploring how they operate and comparing them with 3-axis, 4-axis, and 4+1-axis machining centers, highlighting their importance in modern manufacturing.
What is a 5 Axis CNC Machining Center?
A 5 axis cnc machining center is a highly precise numerical control machine that can perform synchronized operations on five different axes. Compared to traditional 3-axis machining centers, a 5 axis machining center offers greater flexibility and accuracy, enabling it to handle complex angles and geometries. This makes it ideal for high-precision and complex parts manufacturing in industries like aerospace, automotive, and medical equipment.
The Basic Concept Of A 5 Axis CNC Machining Center
The core principle of a 5 axis cnc machining center lies in its ability to move and rotate the tool in five different directions. These five axes include three linear axes—X, Y, Z—and two rotational axes—A/C or B/C axes. The coordination of these axes allows operators to complete multi-angle cutting in a single process without repositioning the workpiece, significantly enhancing processing efficiency.
Units
- X, Y, Z linear axes: corresponding to horizontal, vertical, and longitudinal movements of the workpiece.
- A/C or B/C rotational axes: controlling the tilting and rotation of the workpiece, allowing for multi-angle cutting.
- CNC control system: responsible for coordinating the movement of the tool and workpiece, ensuring machining accuracy.
- Tool-changing mechanism: automatically switches tools according to machining needs, adapting to complex processing requirements.
How Does A 5 Axis CNC Machining Center Work?
A 5 axis cnc machining center operates simultaneously on three linear axes and two rotational axes, allowing multi-surface machining. The cnc equipment controls movements based on the code generated by CAD/CAM systems (such as G-code or M-code), ensuring the tool follows the designed path with precision. CAD handles part design, while CAM is responsible for generating the toolpath and converting it into instructions that the machine can recognize.
Motion control and toolpath
Programming for 5 axis machining centers is highly complex and requires the use of CAD/CAM systems for design and post-processing. Post-processing converts the toolpaths generated by CAD/CAM into code that the machine can accept. This process ensures that each toolpath is precise, enabling 5 axis cnc machining centers to complete machining operations efficiently and accurately.
Advantages Of 5 Axis Machining
The main advantages of 5 axis machining centers lie in their high precision, versatility, and efficiency. Here are its key advantages:
- Improved accuracy: multi-surface machining can be completed in a single setup, reducing errors caused by repositioning and ensuring precise machining each time.
- Reduced processing time: a 5 axis machining center can handle multiple surfaces simultaneously, reducing the need for multiple clamps and repositions, significantly cutting processing time.
- Reduced fixture requirements: since the tool can reach the workpiece from multiple angles, complex fixtures are not needed, reducing fixture costs.
- Flexibility in handling complex parts: a 5 axis cnc machining center can handle geometrically complex parts, such as undercuts and curved surfaces, making it especially suitable for industries like aerospace and medical devices that require high precision.
Types Of 5 Axis Machining Centers
- Head/Head configuration (swing head with head rotational axis): suitable for large workpieces, with the rotational axis on the spindle head, effectively avoiding tool interference and improving machining stability.
- Table/Head configuration (swing head with rotating table): one rotational axis is located on the spindle head, and the other on the worktable, offering high flexibility for multi-angle machining of small to medium workpieces.
- Table/Table configuration (tilting rotary table): both rotational axes are on the table, suitable for complex undercut structures and small or lightweight workpieces.
Comparison Between 5 Axis CNC Machining Centers And 3 Axis, 4 Axis, Or 4+1 Axis CNC Machining Centers
Traditionally, when we talk about machining centers, we usually refer to the typical 3 axis vertical machining center (3 axis VMC), which cuts along the X, Y, and Z axes. These machines feature a vertically oriented spindle that approaches the workpiece from above, making them ideal for manufacturing most geometric shapes and simple parts. However, when it comes to non-traditional shapes or workpieces with deep cavities that are difficult to process, 3 axis machining centers may face difficulties, requiring the use of special fixtures and repeated repositioning, which reduces processing speed and increases labor and costs.
5 axis cnc machining centers, in addition to the X, Y, and Z linear axes, also feature two rotational axes, enabling tools to cut from multiple angles and directions, providing more flexible and comprehensive machining capabilities.
Applications Of 5 Axis Machining
5 axis cnc machining centers are widely applied due to their high precision and flexibility in handling complex parts. Commonly machined parts include:
- Box-type parts: multi-surface machining improves precision.
- Complex surfaces: such as turbine blades and propellers.
- Irregular-shaped parts: machining of non-standard shaped parts.
- Disc-type parts: such as drone parts and motor covers.
- Special processing: complex parts for specific industries.
Major application industries include energy, aerospace, automotive, mold manufacturing, machine tools, and shipbuilding. 5 axis machining center Manufacturers have significantly improved manufacturing efficiency, making 5 axis machining centers ideal for high-precision complex parts while reducing fixture requirements.
As a major breakthrough in modern manufacturing technology, 5 axis cnc machining centers play a critical role across industries due to their flexibility, high precision, and multi-angle machining capabilities. Whether in aerospace, automotive, medical device manufacturing, or energy and mold industries, 5 axis cnc machining centers can handle complex workpieces, improve production efficiency, and reduce costs. With continuous technological advancements, 5 axis cnc machining centers will remain essential equipment in manufacturing, providing robust support for more efficient and precise production.
Campro Machinery's 5 axis product series offers a variety of models to meet the required worktable sizes, ranging from Ø170 mm to Ø1,250 mm. Our professional pre-sales technical team provides comprehensive product evaluations and equipment selection recommendations tailored to our customers' needs. In addition, we offer sample machining tests and improvement suggestions to ensure customers receive the best production solutions. No matter what machining challenges you face, Campro Machinery’s technical expertise will help you achieve efficient and precise production goals.
Contact us now to learn how 5-axis CNC machining technology can enhance your production efficiency and give you a leading edge in the industry!