Efficiency of CNC Turn-Mill in Precision Machining
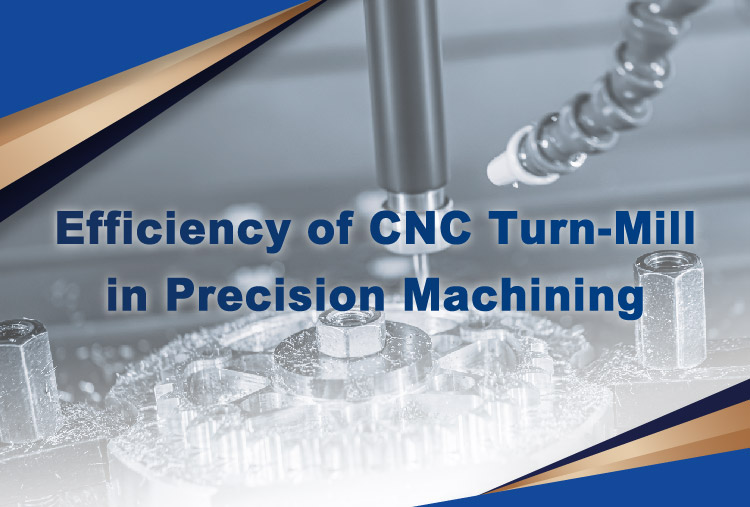
Overview of CNC Turn Mill Center
In the era of thriving smart manufacturing, the maturity of machining technology has led to the rise of multi-axis and compound machining center. Among them, the CNC turning and milling center, as a type of compound machining equipment, combines the functions of a lathe and a milling machine, becoming an indispensable tool in the manufacturing industry. CNC turning and milling center represent the capability to achieve turning, milling, drilling, tapping, and other multifunctional processes on the same machine, offering high precision and efficient production characteristics.
Role and Significance in Modern Manufacturing
As machine tool technology has matured, there has been a shift towards enhancing the functionality of machine tools. This evolution has led to the development of multi-axis machine tools, giving rise to CNC turn mill center machines. The emergence of these machines has not only increased the flexibility of manufacturing but has also added diversity to production. The introduction of CNC turn mill center machines has transformed traditional production methods, bringing about a more efficient, flexible, and economical mode of production in modern manufacturing. The application of this technology not only enhances the competitiveness of enterprises but also propels continuous innovation and progress in the manufacturing industry.
Advantages of CNC Turn Mill Center
CNC turn mill center machines offer significant advantages to the manufacturing industry with features that include completing multiple processes in one clamping, saving space costs, and improving processing efficiency.
Reduced Clamping Frequency, Improved Machining Accuracy:
The turn mill center can accomplish multiple processing steps in one clamping, reducing the frequency of clamping. This effectively avoids error accumulation resulting from the conversion of positioning datum.
Reduced Machine Footprint, Lower Processing Costs:
The compact and aesthetically designed shape of turn mill center improves space utilization, reducing the machine's footprint. This not only enhances the equipment's aesthetics but also saves on processing costs, providing customers with a more economically viable solution.
Streamlined Product Processing, Enhanced Processing Efficiency:
By installing various special cutting tools on turn mill center machines, there is a reduction in tool-changing time. The new cutting tool layout facilitates the completion of multiple processing steps in one clamping, thus improving processing efficiency.
Application of Turn Mill Center
CNC turning and milling center machines find wide-ranging applications suitable for various scenarios requiring intricate workpieces. They are not only adept at handling high-precision fields such as aerospace, medical biology, energy, etc., but also showcase robust application capabilities in areas like the machining of automotive components. The distinctions between turn mill machines and lathe machines are as follows:
1. C-Axis functionality in the spindle, enabling both speed- and position-oriented control.
2. Live tool turret with milling capability; the tools themselves have milling capabilities.
3. Multiple feed axes, including X, Z, and C; some may even include Y-axis and C2 axis (secondary spindle).
4. Capability for radial and axial direction turning and milling machining.
Conclusion
In conclusion, the emergence of turning and milling compound machines, especially CNC turning and milling center machines, has sparked a revolution in manufacturing. These machines not only meet the modern manufacturing demands for high precision and efficiency but also bring greater flexibility and diversity to the development of the manufacturing industry. The application of this compound machining technology undoubtedly continues to lead the manufacturing industry towards higher levels of advancement in the future.