Exploring the Versatility of Gantry Robots in Industrial Automation
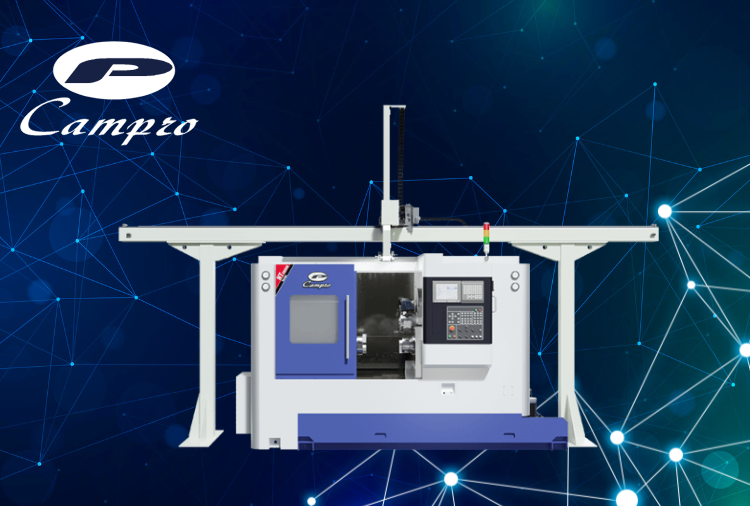
Introduction
Industrial automation has revolutionized modern manufacturing, driving efficiency, cost savings, and precision. As companies increasingly turn to robotic solutions, understanding the versatility of gantry robots is crucial. These robots, characterized by their Cartesian coordinate system, offer unique advantages in factory settings. From their scalability and adaptability to their precision and cost-effectiveness, gantry robots play a pivotal role in enhancing production processes. This article explores the various aspects of gantry robots, focusing on their application, advantages, and impact on industrial automation.
Common Types of Industrial Robots
As technology advances, factory automation has become integral to modern manufacturing, enhancing production efficiency, reducing costs, and ensuring precision. An increasing number of companies are considering the introduction of robotic arms to assist in factory operations. These robots, available in various shapes and sizes, handle repetitive and hazardous tasks. They are classified based on design into Cartesian, articulated, cylindrical, delta, polar, SCARA, and collaborative robots, meeting diverse industrial production line requirements and applicable scenarios. Gantry robots offer scalability, allowing them to be adjusted according to production needs, which enhances flexibility and cost-effectiveness. They are ideal for their overall top-down working space.
What Are Gantry Robots?
Gantry robots are characterized by their simple Cartesian coordinate structure. They move in a manner where each direction forms a 90-degree angle with the previous arm segment. This system typically utilizes coordinates such as X, Y, Z to indicate the direction of movement, enabling it to operate within the range of each coordinate. Gantry robot arms typically move along linear paths, defining a three-dimensional cubic envelope of space in which they can operate.
Gantry Robot Applications with CNC Metal Machines in a Shop-floor
Gantry robot arms are automated systems used in manufacturing that operate on a Cartesian coordinate system, with two linear paths intersecting at right angles to form the working plane (typically denoted as X and Y axes). By adding a third axis (Z axis), the system gains depth, enabling the end-of-arm-tool to work within a three-dimensional cubic envelope.
One of the primary applications of gantry robots in a shop-floor setting is in conjunction with CNC (Computer Numerical Control) metal machines. These robots excel in material handling tasks, playing a crucial role in streamlining workflow and enhancing overall productivity.
One of the key advantages of gantry robots is their versatility. Customers have the flexibility to customize stroke lengths to suit specific requirements, such as the size of the machine, the length of the workstation, and the layout configuration, whether it involves one robot per machine or one robot servicing multiple machines.
Gantry robots can operate either individually or in a series, depending on the production needs. Unlike 6-axis robots that are designed to handle heavier workpieces, gantry robots are better suited for lighter workpiece weights.
Summarize Advantages of Gantry Robot
Precision: Gantry robots operate on a Cartesian coordinate system, ensuring precise movements in three-dimensional space. This precision is crucial for intricate manufacturing processes.
Flexibility: These robots can be customized to fit various production line layouts and machine sizes, offering flexibility in adapting to different manufacturing environments.
Efficiency: By automating material handling tasks, gantry robots can significantly improve workflow efficiency, leading to increased productivity and reduced cycle times.
Cost-effectiveness: Gantry robots are typically more cost-effective than their 6-axis counterparts, making them an attractive option for manufacturers looking to optimize their production processes without breaking the bank.
Safety: With the ability to handle lighter workpiece weights, gantry robots provide a safer working environment for operators compared to heavy-duty robots.
Conclusion
In conclusion, gantry robots are instrumental in revolutionizing industrial automation, offering a wide array of benefits that significantly impact manufacturing processes. From their precision movements in three-dimensional space to their adaptability and cost-effectiveness, gantry robots have proven to be invaluable assets in modern manufacturing environments.
One of the standout examples of gantry robot excellence is the CRG Series Gantry Robot from Campro. Specifically designed to complement CNC machines, the CRG Series offers exceptional flexibility and scalability. Its ability to handle material handling tasks with precision and efficiency makes it a standout choice for optimizing workflow and enhancing productivity.
The CRG Series, which is designed to collaborate with Campro CNC machines, offers high flexibility and scalability. Its versatility allows for seamless integration into various automated production lines, providing customers with the freedom to customize stroke lengths and adapt the robot to specific requirements. This adaptability, coupled with its advanced capabilities, makes the CRG Series a top choice for high-efficiency shop floors.
Overall, gantry robots, exemplified by the CRG Series, play a crucial role in streamlining material handling tasks, improving workflow efficiency, and ensuring consistent and accurate production processes. As technology continues to advance, gantry robots are poised to play an even more significant role in shaping the future of industrial automation.