Revolutionizing Smart Manufacturing: AI-Driven CNC Machining Technology Part 2
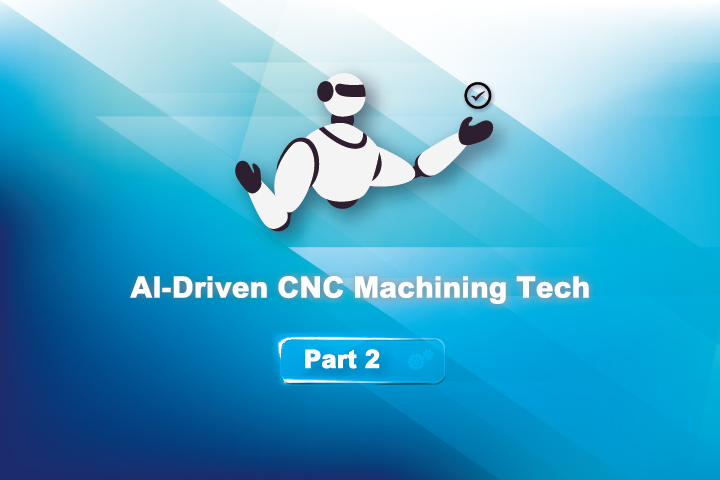
Building on the previous discussion, we will delve deeper into the core role and implementation of AI technology in CNC machining centers.
The application of Artificial Intelligence (AI) in the field of CNC machining is not just a technological innovation but an industrial transformation. The core role of AI technology lies in its ability to significantly enhance machining efficiency, precision, and adaptability, all achieved through intelligent data analysis and machine learning.
Firstly, AI can optimize the machining paths of CNC machines through data analysis. In traditional CNC machining, setting machining parameters often relies on the operator's experience and intuition. While this method is feasible, it may lack precision or efficiency when dealing with complex or unfamiliar machining tasks. AI technology, by analyzing past machining data, can accurately predict the optimal machining parameters, such as spindle speed, feed rate, and cutting depth, and automatically adjust these parameters to suit different material properties and machining requirements.
III. Enhancing Production Efficiency and Reducing Waste
In modern manufacturing, enhancing production efficiency and reducing resource waste are crucial goals for the sustainable development of enterprises. The application of Artificial Intelligence (AI) in CNC machining technology provides an efficient and sustainable solution to achieve these goals. AI not only improves operational efficiency but also reduces material and energy waste through intelligent process optimization.
Firstly, AI can significantly enhance the production efficiency of CNC machines. Through predictive maintenance and fault warning systems, AI can analyze machine operation data to predict mechanical failures and maintenance needs, thereby reducing unexpected machine downtime. This predictive capability not only ensures optimal machine operation but also effectively extends equipment lifespan, reducing economic losses caused by sudden failures. Additionally, AI's real-time adjustment functionality can automatically optimize machine operating parameters, such as speed and cutting force, during the machining process to adapt to different conditions. This not only increases production speed but also reduces material waste and energy consumption.
Secondly, AI plays a critical role in reducing material waste. Through precise data analysis, AI can optimize cutting paths and material configurations to ensure the most efficient use of every piece of raw material. This not only enhances material utilization but also reduces waste generated during the production process. In the machining of high-value materials, such as aerospace aluminum or titanium alloys, this optimization is particularly important as material costs represent a significant portion of the overall production cost.
Moreover, AI excels in energy management. It can intelligently regulate machine energy consumption based on actual production demands, such as automatically lowering energy usage during low-load periods or maximizing the use of low-energy modes without affecting production efficiency. This intelligent energy management not only reduces operational costs for enterprises but also contributes to environmental protection.
In summary, The CNC machine application of AI technology brings considerable economic and environmental benefits by enhancing production efficiency and reducing waste. This allows enterprises to respond more effectively to market changes and demands, driving the entire industry towards a more sustainable and intelligent future.
IV. Quality Control and Process Monitoring
In modern manufacturing, ensuring product quality and monitoring the stability of the production process are of paramount importance. The CNC machine application of AI technology not only enhances production efficiency but also significantly improves the accuracy of quality inspection and the real-time monitoring of processes. This technological innovation makes the manufacturing process more reliable, greatly reduces the production of defective products, and ensures the consistency of product quality.
AI systems can utilize advanced sensing technologies and data analysis to monitor the machining status of CNC machines in real time. This includes monitoring tool wear, the dimensional accuracy of workpieces, and mechanical feedback during the machining process. With this data, AI can instantly detect any abnormalities that could lead to quality issues, such as excessive tool wear or deviations in machining parameters. Once these issues are detected, AI systems can automatically adjust machine parameters or pause the machining process until the problems are resolved, ensuring that every product meets high-quality standards.
Furthermore, the application of AI enhances product consistency during the manufacturing process. In large-scale production, even minor variations can result in significant quantities of non-conforming products. AI systems can learn and record the successful machining conditions of each production run and apply these conditions to subsequent production, ensuring that all products meet the same high standards. This not only reduces quality fluctuations but also boosts customer confidence in the product quality.
AI also plays a crucial role in reducing human errors. In traditional CNC operations, human factors often lead to product quality issues. The introduction of AI allows for the automation of many decisions and operations, reducing the likelihood of human errors. For instance, AI systems can automatically execute complex machining programs, reducing the need for manual adjustments by operators, thereby lowering error rates and enhancing overall product quality.
In summary, the application of AI technology in quality control and process monitoring brings revolutionary improvements to the CNC machining field. Through real-time monitoring and intelligent adjustments, AI not only enhances product quality but also increases the stability and reliability of the manufacturing process. For modern manufacturing industries striving for defect-free production and high customer satisfaction, this holds immeasurable value.
conclusion
Through these advanced functionalities, AI not only elevates the technical level of CNC machining but also greatly enhances the intelligence and automation of production processes. As these technologies continue to develop and be applied, AI will play an increasingly important role in the field of CNC machining, driving the manufacturing industry toward a more efficient and precise future.
Building on these advancements, the next part of our discussion will focus on how AI technology enhances production efficiency, reduces waste, and ensures superior quality control in CNC machining processes.