What is CNC turning Machine
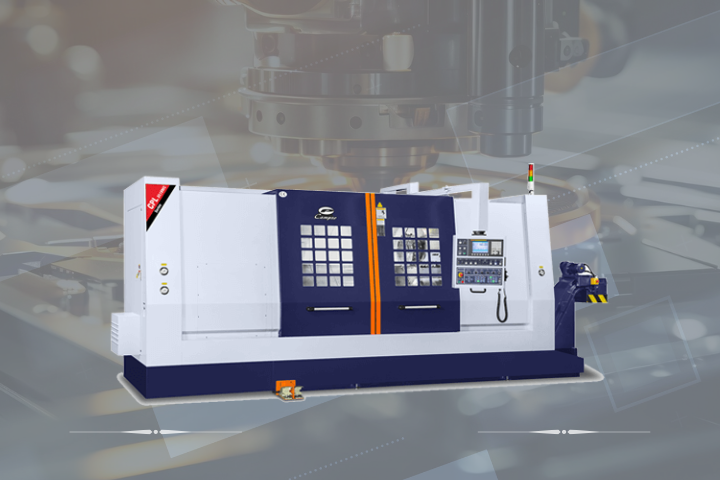
In this article, we delve into the world of CNC Turning machine, exploring their key components, functionalities, and the crucial role they play in modern manufacturing. A Precision Lathe, or Computer Numerical Control lathe, is a specialized machine tool used in metalworking and metal spinning. It operates by rotating a bar of material to perform various operations such as cutting, drilling, and shaping, all controlled by computer programming.
CNC turning machine precision lathes come in two primary types: horizontal turning machine and vertical turning center. Horizontal lathes have a horizontally mounted spindle, while vertical lathes have a vertically mounted spindle. Each type offers distinct advantages depending on the specific application.
The core principle of a CNC lathe involves clamping the workpiece with a chuck and rotating it with the spindle. A tool turret holds an array of cutting tools that can be indexed and fed to the workpiece, enabling precise material removal and shaping. Known for their speed, accuracy, and versatility, CNC lathe machines are indispensable in modern manufacturing processes.
Additionally, we explore the difference between CNC lathes and CNC turn mill centers within a CNC Turning Center. While CNC lathes operate primarily on two axes, performing basic turning operations, CNC turn mill centers offer a broader range of capabilities. They can operate on multiple axes, perform various operations beyond turning, and often feature a sub-spindle for enhanced machining capabilities.
Overall, CNC lathe machines are essential in modern manufacturing, offering precise and efficient production capabilities that meet the demands of today's industries.
What is a CNC Lathe Machine
A CNC lathe machine, short for Computer Numerical Control lathe machine, is a type of machine tool used in metalworking and metal spinning. It rotates a bar of material to perform various operations such as cutting, drilling, and shaping, controlled by computer programming. CNC lathes are integral to modern manufacturing, offering precise and efficient production capabilities.
There are two main types of CNC lathes: horizontal and vertical. Horizontal CNC lathes have the spindle mounted horizontally, while vertical CNC lathes have the spindle mounted vertically. Each configuration offers its own advantages depending on the specific application.
The basic principle of operation of a CNC lathe involves the rotation of the workpiece, which is clamped by a chuck and rotated by the spindle. A tool turret holds a variety of cutting tools that can be indexed and fed to the workpiece to remove material and create the desired shape. CNC lathe machines are known for their speed, accuracy, and versatility, making them essential in modern manufacturing processes.
What is The Difference between CNC Lathe and CNC Turn Mill?
CNC lathes and CNC turn mill centers differ significantly in functionality within a CNC Turning Center.
CNC lathes are relatively simple machines that operate primarily on two axes (X and Z), performing tasks such as turning and facing. They are limited compared to CNC turn mill centers.
In contrast, CNC turn mill centers offer a wider range of capabilities. They can operate on multiple axes, including the standard X and Z axes, as well as additional axes for milling functions. This allows them to perform a variety of operations beyond basic turning, such as drilling, milling, knurling, boring, tapering, and threading.
Additionally, CNC turn mill machines can have a sub-spindle, further enhancing their capabilities. This sub-spindle can perform additional machining operations on the workpiece without repositioning.
It's worth noting that CNC turn mill centers are sometimes referred to as CNC Turning and Milling Centers or Multi-Tasking Machining Centers, highlighting their ability to perform both turning and milling operations in a single setup.
In summary, while CNC lathes are limited to basic turning operations, CNC turn mill centers are more versatile and can perform a variety of complex machining tasks, making them ideal for applications that require multiple machining operations within a single machine setup.
The table below illustrates the differences between CNC Lathe and CNC Turn Mill:
number of linear axis | Rotary axis feasibility | Sub-spindle feasibility | Milling function feasibility | Y-axis feasibility | Turret | |
---|---|---|---|---|---|---|
CNC Lathe | 2 | X | V | X | X | Hydraulic or Servo |
CNC Turn Mill | 2 or more | V | V | V (Due to the live turret) |
V | Servo power (Live Turret) |
Conclusion:
In conclusion, A CNC turning machine, whether horizontal or vertical, play a crucial role in modern metalworking and manufacturing processes. Their ability to rotate a bar of material and perform various operations with precision and efficiency makes them indispensable in the industry.
The difference between CNC lathes and CNC turn mill centers lies in their functionality within a CNC Turning Center. While CNC lathes are simpler and operate primarily on two axes, CNC turn mill centers offer a wider range of capabilities, including the ability to operate on multiple axes for complex machining tasks.
As a CNC Lathe Machine Manufacturer, CAMPRO stands out for its innovative designs and high-quality products. CAMPRO CNC Turning Center Series, with their true slant bed design, offer superior rigidity and thermal stability, allowing for heavier cutting with a smaller footprint. From CPL Series to NT Series and VT Series, CAMPRO provides a wide range of machines to meet various manufacturing demands.
Ready to take the next step in precision machining? Contact us today to discuss your CNC turning solution.